Student Biography
Building Statistics
Part 1
General Building Data
Project Team
Building Name
Location
Occupant Name
Project Size
Number of Stories
Construction Dates
Project Cost
Delivery Method
The Lauren
Bethesda, Maryland
1788 Holdings
95,000 SF
7 above grade, 3 below grade (2 parking), 10 total
May 2014 - March 2016
$36 million
Construction Manager at Risk with GMP Contract
Architecture
The Lauren is an extremely high-end residential condominium complex in the heart of downtown Bethesda, Maryland, just steps away from dozens of dining, entertainment and retail locations. This 95,000 square foot, 10 story building has seven levels above grade and three below, including a garden level and two levels of underground parking. The building contains 40 units (34 market rate, 6 MPDU) over eight stories of occupiable space, including a $10.5 million penthouse on the seventh floor, the most expensive condominium unit to ever be sold in the Washington-Metro area. In addition to the units, the building contains several amenities such as a fitness center, wine lounge, full-time concierge and wine sommelier and accessible roof with private patios.

Codes
International Building Code (IBC) 2012
Maryland Building Rehabilitation Code (MBRC)
Americans with Disabilities Act (ADA)
ACI 530/ASCE 5 (Building Code Requirements for Masonry Structures)
AISC 303 (Code of Standard Practice for Steel Buildings and Bridges)
NEC 2005 (Electrical Code)
NFPA 13 (Fire Protection)
Zoning
Historical Requirements
County TS-R
Not Applicable
Building Enclosure
Building Façade:
The building façade consists primarily of two different finishing materials, Terra-Core Stone Panels and Exterior Insulation Finishing System (EFIS). As seen in Detail 9 below, while both are used as exterior finish materials, the Stone Panels are a more prominent feature on the building façade, while the EFIS is typically used on the interior of the balconies. The complete enclosure system is specified in Detail 8 below, consisting of the Terra-Core Stone Panels, Mineral Wool Board Insulation, Fluid applied Air Barrier Membrane and Exterior Gypsum Sheathing.
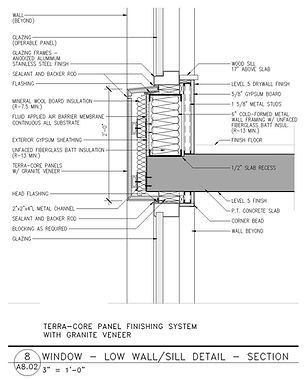

Roofing System:
The main roofing system consists of a Hot-Fluid Applied Protected Membrane Roofing material. As seen in Detail 1 to the right, this is topped with a minimum of R-25 insulation and a structural concrete deck that is sloped to access the roof drains. The design calls for and occupiable roof with private patios and public entertainment areas which the building occupants can freely access. Therefore, the primary roofing system is topped with precast pavers on a pedestal for both durability and aesthetic purposes.


Sustainability Features

The Lauren is striving for Certification under LEED for Homes Midrise 2010. Compared to typical buildings, the exterior façade of the building is design to be especially air-tight to reduce energy usage. This is being verified through the use of a Blower Door Test where a device is placed on the exterior of each unit and all the air is dispelled from the space to determine existing gaps in the façade where air could potentially enter. Additional features include optimized energy performance, a high-efficiency irrigation system and advanced erosion control and waste management during construction.
Part 2
Construction
The construction began with the demolition of three existing buildings. These included a three-story brick building on the south-east corner of the site and two, two story buildings on the north section of the site. Additionally, there were several existing sidewalks and foliage that needed to be removed. For support of excavation, the project used two primary methods: piles/lagging with tiebacks and rakers. Piles were driven along the north, east and south facades, as well as the north half of the west façade. Rakers were required on the south portion of the west façade because an agreement could not be reached with the owner of the adjacent building to place tiebacks under bordering structure. Piles and lagging were the preferred method over the rakers because they became a challenge during the structural phase since the slab on grade and elevated decks needed to

be poured around the rakers and then filled in after they were removed. Once the structure began, a tower crane was erected in the center of the building footprint to transport rebar into the building. A concrete placing boom was also built into the structure to help pump the concrete to the slab where it would be placed. Both of these pieces of equipment were removed shortly after the structure topped out. As the building moved into the enclosure phase, boom lifts arrived on site to help lift the sections of the stone panel façade into place. Finally, during the finishing phase, a material hoist is placed on the south elevation to help transport items throughout the building.
Structure

The Lauren is a ten-story, cast-in-place, post-tensioned concrete structure with three stories below grade, seven above grade and a small penthouse roof. The slab on grade uses 4500 psi, normal weight concrete at 5” thick and is placed over a vapor barrier and 4” of washed gravel. All elevated slabs are made up of 5000 psi, normal weight concrete and are typically 8” thick, with some exceptions where the slab is 9” thick. The structure utilizes both post-tensioned and steel reinforcing with the elevated slabs up through the lobby level and columns using rebar and the elevated slabs from the 2nd level through the roof using the post-tensioned cables. The rebar typically consists of #11 and #14 bars in the slabs and #10 stirrups in the columns. The post-tensioning is done through unbonded cables that must be stressed to a minimum strength of 270 ksi. The slab on grade is reinforced a bit differently using 6x6 pieces of welded wire fabric that are placed within the slab.
Electrical
There is one central electrical room, located on the northwest corner of the Garden Level, which serves the entire building. The electricity enters the building at low voltage through a 4000 amp switchgear. A transformer drops it to a 2000 amp switchgear which serves the majority of the building. The system is sized at 3-phase, 4 wire and 208Y/120V. The switchgear also serves a 50 hp fire pump and a 180 kW emergency generator.
Lighting

In the Lauren, the lighting fixtures are typically standard across all residential units. The most common fixture is an 18 watt recessed LED light that is used across all rooms of the unit. In many of the Foyers, Grand Salons and Master Bedrooms LED cove lighting is used instead of the recessed lighting to allow for higher ceiling heights. Each of the bathrooms are furnished with two 60 watt, T10 wall sconces and an Electric LED mirror, some of which include a built in television. The public areas also used standard lighting fixture including 33 watt LED downlights and 21 or 28 watt, T5 fluorescent cove lighting.
Mechanical

The project uses a fairly typical mechanical system with a split system heat pump and individual air handling units (AHUs). Each condominium unit contains its own mechanical closet and AHU which are all served by rooftop condensing units. There is also a large condensing unit on the roof to serve all the common areas of the building. A unique aspect of the mechanical system is the use of Duct Board as opposed to the typical sheet metal ducts. This provides better insulation for both sound and air flow.
Fire Protection
The fire protection system uses two different alternatives, a wet-pipe sprinkler system and a dry-pipe sprinkler system. The wet-pipe system is from the ground floor up while the dry-pipe system is in all the floors below grade. Each system functions in a completely different way. The wet-pipe system has automatic sprinklers that are attached to piping already containing water so in the case of an emergency the water discharges immediately. The dry-pipe system, however, has piping filled with compressed air. When the sprinkler open the pressure is released, opening a valve and discharging the water.
Transportation
The Lauren has three elevator shafts and two central staircases. All are located in a central core with residential units surrounding it. Of the three elevator shafts there are two passenger elevators and one service elevator. For the more expensive units, residents can get into a passenger elevator on either the parking, garden or
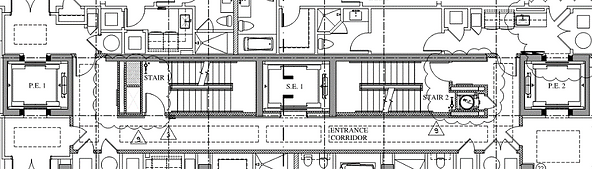
lobby levels that provides private transportation directly to their own foyer outside the entrance to their condo. The service elevator is accessible to all units from all floors and is intended for both guests and residents of the additional units that do not have access to a passenger elevator. Additionally, the service elevator is about 10 SF larger than the passenger elevators so it is a resource for transporting large materials, such as furniture.
Access Security
Since the Lauren is an extremely high-end residential building, there are a variety of access control systems put in place to keep the building secure for all residents. There is a card reader at the main entrance of the building as well as at the entrance to building amenities such as the wine lounge, fitness canter and unit storage. Additionally, there is a proximity card reader in each of the elevators that serves as a key so only residents have access to their units. There are also high-definition cameras in the garage and at the main entrance to monitor who is entering and exiting the building.